Asphalt
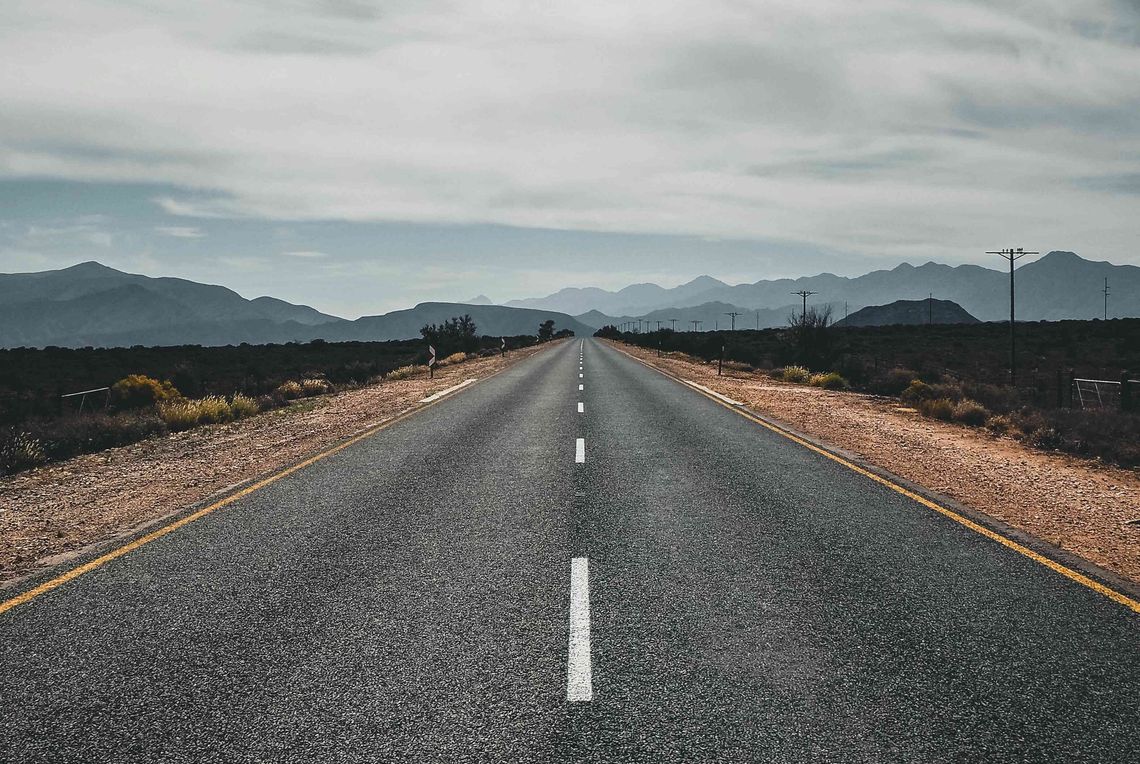
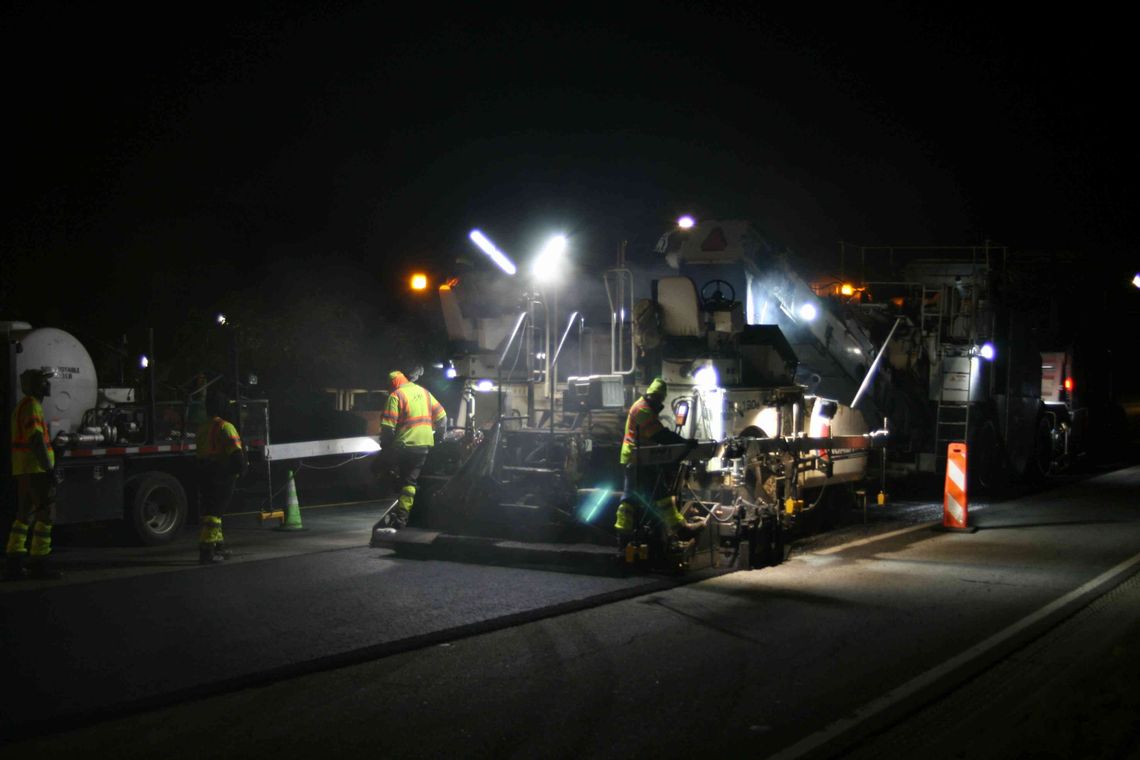
Lehigh Technologies produces a number of products that are used to create the industries most robust Rubber Modified Asphalt (RMA) systems. They are used in the asphalt field (paving, roofing, water barrier membranes, etc.) as an environmentally sustainable direct replacement for synthetic polymers such as SBS and latex. These powders have been approved and used for over a decade by asphalt blenders, contractors, and Department of Transportations (DOTs) to increase performance properties and gain PG advancements in RMA. They are used by many to modify hotmix/warmmix via the “Dry/Plant Blended Process” and liquid bitumen through the “Terminal Blend/Wet Process”. See more details below.
“TERMINAL BLEND/WET PROCESS" LIQUID BITUMAN ASPHALT
MicroDyne™
Ground tire rubber (GTR) and micronized rubber powder (MRP) products are engineered powders produced from end-of-life tires. The industry recognizes our powders as being the most consistent, highest quality and free flowing powders in the market. You will receive the same particle distribution, high quality (no metal, no fiber) and tire genetics with every pound of powder received which is key in making stable and reliable modified binders.
Rheopave™
Is a proprietary formulation of polymers and other components designed for applications in the modification of asphalt binders and for stabilizing ground tire rubber (GTR) in RMA blends.
It disperses easily and is designed to be used together with Lehigh’s rubber powder in RMA systems to improve dynamic shear rheometer (DSR) performance (lower phase angle), improve multiple stress creep recovery (MSCR) performance (higher percent recovery), and improve GTR storage stability (lower delta-T). When properly formulated, Rheopave+/GTR binders meet all performance requirements for polymer-modified binders. The chemistry is independent of Styrene-butadiene Styrene (SBS) and thus is not tied to SBS supply, feedstock or volatile price indexing.
RMA is a growing application for MRP in the United States and around the world. RMA is already employed or being trialed in over 35 states and nations such as China, Germany, Australia, Korea and Spain.
“DRY/PLANT BLENDED” PROCESS HOTMIX/WARMMIX ASPHALT
The primary function of Lehigh’s MicroDyne 400-TRXP™ dry blend is to economically modify asphalt (+ two grade bumps to create a PG76-22) at the contractor site by means of an environmentally sustainable, low-cost hybrid system.
Customized blend of MicroDyne 400-TR (40 mesh ground tire rubber) and Rheopave (performance polymer additive)
Lehigh partner labs provide custom formulations with your base asphalt which is designed to meet State specific DOT requirements. Lehigh will then dry blend Rheopave and MicroDyne 400-TR into a homogeneous mix based on this formulation at our Atlanta, GA facility.
MicroDyne 400-TRXP dry blend is supplied directly to the producer/contractor in 2,000 LB super sacks where it is added like a fine aggregate during mix production. It is typically added via a weight loss machine though the RAP collar.
This system which is designed to meet PMA specifications has been employed in large volume rubber modified asphalt projects throughout the USA for over a decade. Approximately 1 million tons of US asphalt mix have been paved utilizing the MicroDyne 400-TRXP system through 2022.
RMA Produced with Lehigh Product Benefits
Improved durability and increased rutting and crack resistance, which means less maintenance.
Increased safety. Some studies show that using RMA boosts traction and reduces the risk of skidding.
More cost-effective. Using RMA in road maintenance reduces reliance on oil-based materials and avoids the oil-price roller coaster. RMA also helps maintain a blacker surface, which retains heat better and therefore decreases salt and sand use in winter months.
Reduced traffic noise. Studies show that roads made with RMA are significantly quieter than those made with regular asphalt surfaces.
Reduced environmental footprint. Using Lehigh's micronized rubber powders reduces use of oil-based materials and diverts end-of-life tires and post-industrial rubber from landfills.
For more information on the benefits of using RMA in roads, visit the Rubberized Asphalt Foundation website.
Lehigh collaborates with asphalt modifiers, manufacturers, and contractors to ensure that their asphalt cement formulations meet stringent Federal Highway Administration and DOT safety and performance specifications. MRP is optimized for ease of use, with consistent particle size, extreme quality, and first-in-class flowability, which are essential for RMA performance and cost effectiveness.
RESEARCH
To better understand the interaction between MRP and asphalt, Lehigh Technologies embarked on a number of studies with the National Center for Asphalt Technology (NCAT):
Effect of ground tire rubber particle size and grinding method on asphalt binder properties
Effect of ground tire rubber particles on open-graded mixture performance
With over a decade of successful commercial use and strong technical support provided by these NCAT studies, the utilization of Cryogenic GTR and MRP in asphalt binder modification and mix designs has grown substantially. Armed with this information, over half a dozen states have modernized their Rubber Modified Asphalt Specifications to incorporate the use of cryogenically ground rubber powders.
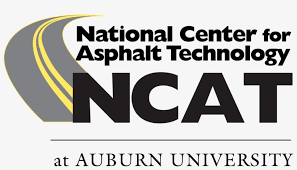
Rubber is a product that provides long-term supply. [Using RMA] is a more cost-effective and competitive way to modify asphalt, and it provides an outlay for scrap tires that may otherwise end up in landfills."
Lehigh partnered with the National Center for Asphalt Technology to perform research to better understand the interaction between MRP and asphalt. This partnership resulted in two published studies:
Effect of Ground Tire Rubber Particles on Open-Graded Mixture Performance, December 2013.
Effect on Ground Tire Rubber Particle Size and Grinding Method on Asphalt Binder properties, October 2012.
For more detailed information and samples please contact Ryan Alleman
CONTACT CUSTOMER SERVICE
678.495.2244
customerservice@lehightechnologies.com
Click the link for additional contacts
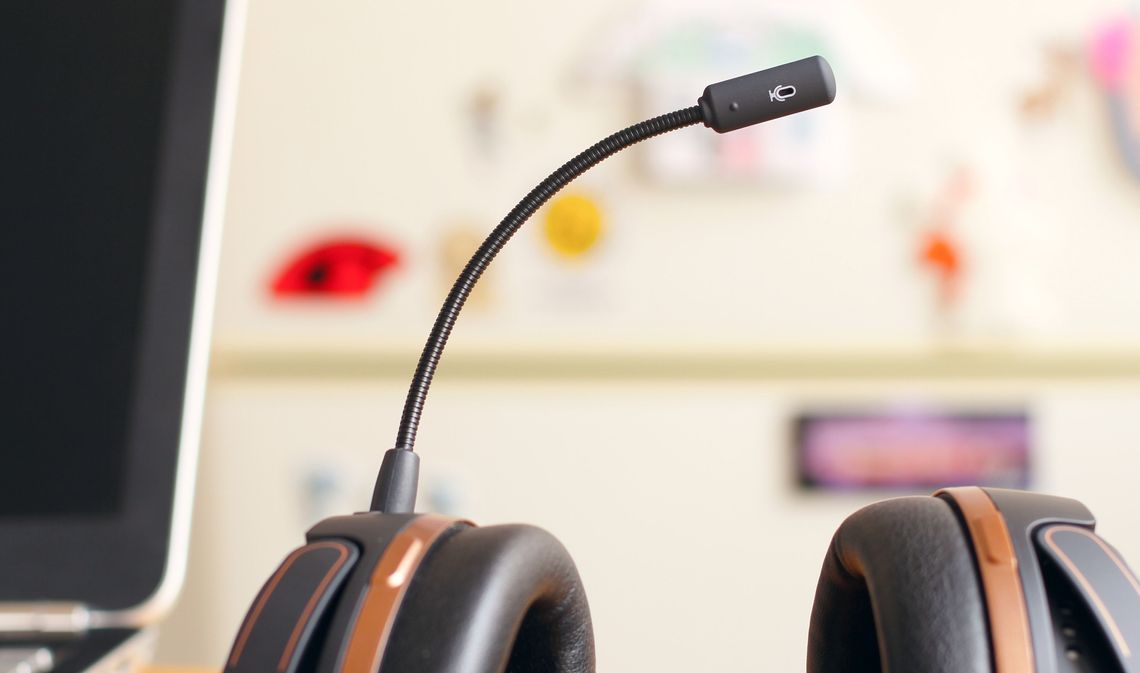